The following three scenarios will clearly demonstrate that electrical installation technology should not be considered after design. Electrical installation technology is a necessary engineering consideration and should be included in the total cost calculation. The following three scenarios will clearly demonstrate that electrical installation technology should not be considered after design. Electrical installation technology is a necessary engineering consideration and should be included in the total cost calculation.
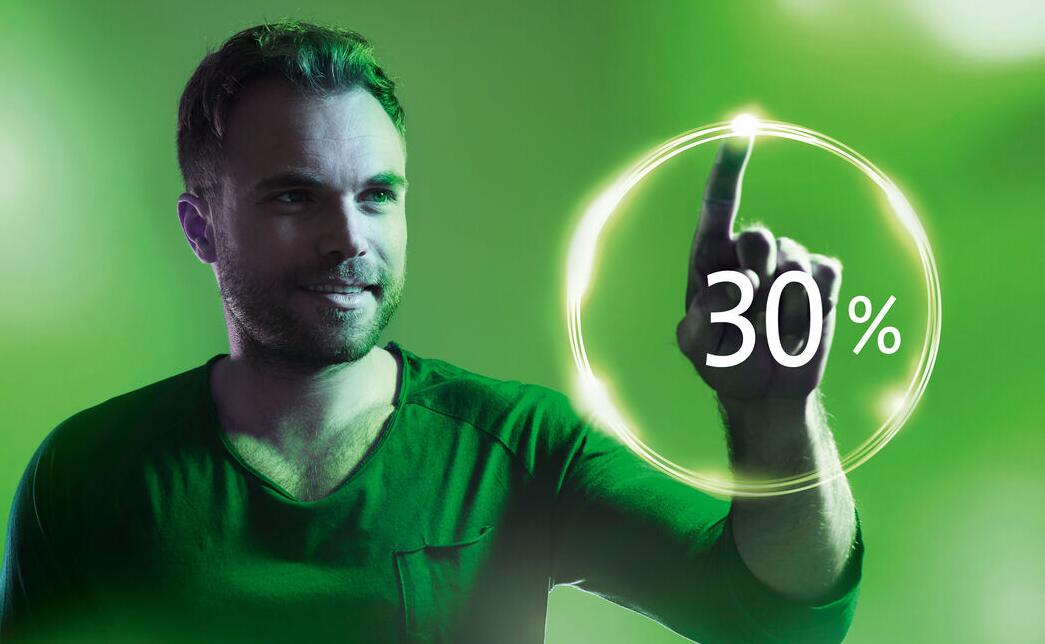
Long ago, electrical installation in machine manufacturing remained in the traditional way. All control technologies are housed in the control cabinet and connected to sensors and actuators in the field via large junction boxes. Compatibility between components makes the system error-prone, and expensive installation and debugging must be repeated from one machine to another. Standardized plug connections are rare, and when connector connections appear, they have to be reconfigured manually, which is an extremely tedious process.
In recent years, power and data have been distributed in separate junction boxes around the machine. This moves the classic parallel wiring method from the control cabinet to the field. While this does reduce installation effort, the extra terminal block means more potential sources of error and wiring errors between the control cabinet and peripherals. Short circuits and overloads, if they occur, can lead to difficult and time-consuming troubleshooting tasks, resulting in long downtime and production failures.
Today, the IO layer is located near the actuators and sensors. This greatly reduces the size of the control cabinet. Advantages of this approach include plug-in system components and IP67 rated, vibration-resistant, fully tested prefabricated connectors of various lengths. Electrical installation is simpler and installation time is greatly reduced. Wiring errors are virtually eliminated, making the debugging process faster and less annoying.
So what does the future hold? Whether you take a long-term view or not, significant cost savings are not possible without a systematic approach and targeted use of installation techniques. Moore Electronics' tailor-made installation concepts and components not only reduce overall costs by up to 30%, but also enable the system to benefit both mechanical engineers and machine operators by benefiting from a range of technological advances, including innovative diagnostic capabilities.